Cost-effective, reliable fine screening technology
Sieve Bend Screens are custom-designed to separate solids from liquids in various applications, including food processing, pulp and paper, waste water cleanup, surface water intakes, corn wet milling, coal preparation, and gold recovery. The gravity-fed Sieve Bend design provides for effective dewatering and allows the solids to slide off the end of the screen surface.
Unlike traditional flat screens, Sieve Bend Screens utilize a curved profile wire or wedge wire design, allowing for higher throughput, improved drainage, and reduced maintenance costs. Their gravity-fed operation ensures seamless separation, with solids sliding off the screen surface while liquids pass through efficiently.
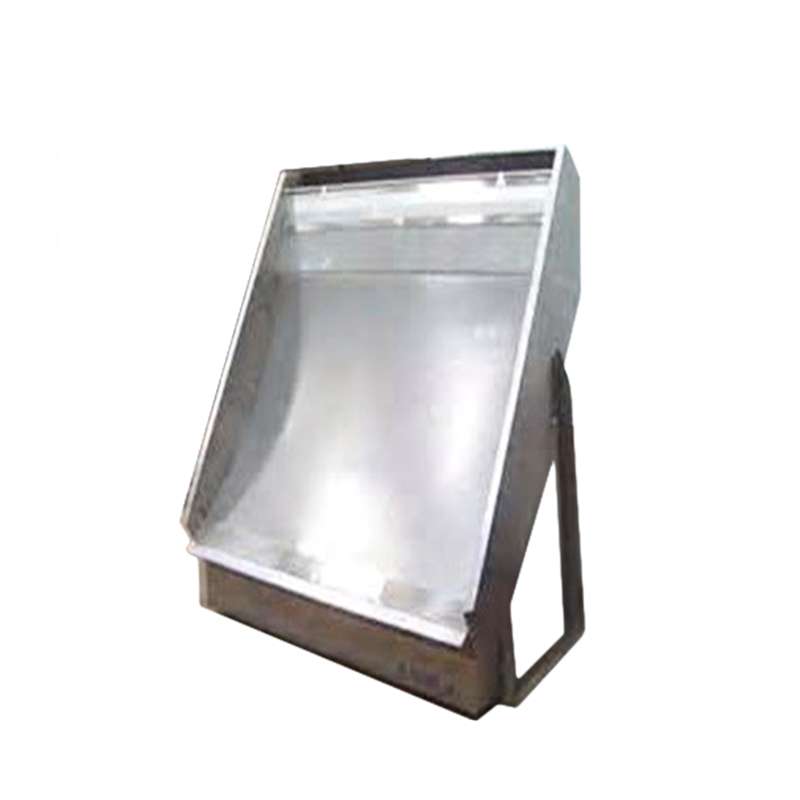
How Sieve Bend Screens Work?
1. Curved Screen Design for Enhanced Performance
The unique concave curvature of Sieve Bend Screens plays a crucial role in their efficiency. As slurry flows over the screen:
Centrifugal and gravitational forces push liquids through the openings.
Solids are retained on the surface and discharged at the bottom.
The Coanda effect further enhances drainage by directing liquid flow along the screen’s curve.
This design ensures higher capacity compared to flat screens, reducing clogging and improving longevity.
2. Wedge Wire & Profile Wire Construction
Sieve Bend Screens are constructed using:
Wedge wire panels: Durable, corrosion-resistant, and customizable for different slot sizes.
Stainless steel or special alloys: For extended wear life in abrasive environments.
Reinforced end bars: For structural stability and easy installation.
The perpendicular alignment of screen openings to the flow direction maximizes separation efficiency.
Key Advantages of Sieve Bend Screens
1. Superior Fine Fiber & Solid Removal
Higher fine fiber recovery (critical for paper recycling).
Effective removal of abrasive solids (sand, glass, plastics, foundry slag).
2. Increased Flow Rates & Reduced Downtime
Optimized curvature prevents blockages, ensuring continuous operation.
Low maintenance requirements due to self-cleaning action.
3. Custom Solutions for Cost Efficiency
Tailored slot sizes for specific separation needs.
Special alloys (e.g., 304L, 316L, duplex steel) for corrosive or high-wear applications.
Surface treatments (e.g., polishing, coatings) to enhance durability.
4. Environmentally Sustainable Dewatering
Reduces water consumption by improving liquid recovery.
Minimizes waste disposal costs through efficient solids capture.
Industrial Applications of Sieve Bend Screens
1. Wastewater Treatment & Pretreatment
Municipal & industrial plants use Sieve Bends for:
Grit removal (sand, gravel).
Primary screening before biological treatment.
Sludge dewatering to reduce disposal volumes.
2. Food & Beverage Processing
Corn wet milling: Starch and gluten separation.
Meat processing: Byproduct recovery and wastewater filtration.
Dairy & brewing: Solids removal from process water.
3. Pulp & Paper Industry
4. Mining & Mineral Processing
5. Surface Water Intake Screening
Prevents debris from entering cooling systems in power plants.
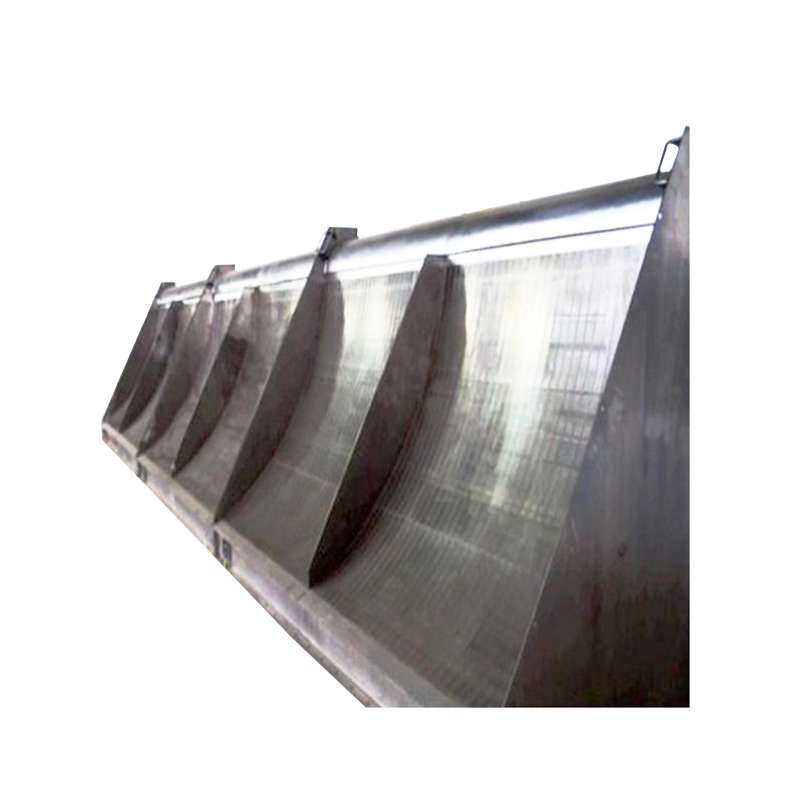
Choosing the Right Sieve Bend Screen for Your Operation
1. Slot Size Selection
Fine separation (0.1mm - 0.5mm): For fiber and micro-solids.
Medium (0.5mm - 1.5mm): General wastewater screening.
Coarse (1.5mm - 3mm+): For heavy solids like gravel.
2. Material Considerations
304 Stainless Steel: Standard corrosion resistance.
316 Stainless Steel: For high-chloride environments.
Duplex Steel: Extreme abrasion resistance.
3. Installation & Maintenance Tips
Optimal feed distribution ensures even wear.
Regular inspection prevents unexpected failures.
Pressure washing can extend screen life.
Why Industries Trust Our Sieve Bend Solutions
With decades of expertise in static dewatering technology, we provide:
Custom-engineered screens for unique challenges.
Fast lead times & global supply chain support.
Technical assistance for optimal performance.
Conclusion: Enhance Your Dewatering Process with Sieve Bend Screens
Whether you're in wastewater treatment, food processing, mining, or pulp & paper, Sieve Bend Screens offer a durable, efficient, and cost-effective solution for solid-liquid separation. By leveraging advanced wedge wire technology, gravity-fed operation, and customizable designs, industries can achieve higher productivity, reduced waste, and lower operational costs.
Contact our team today to discuss how our Sieve Bend solutions can optimize your process!
sales@uboscreen.com
86-18032153916
FAQs About Sieve Bend Screens
Q: What is the typical lifespan of a Sieve Bend Screen?
A: Depending on material and application, screens last 2-10 years with proper maintenance.
Q: Can Sieve Bends handle high-temperature slurries?
A: Yes, heat-resistant alloys are available for extreme conditions.
Q: Are custom shapes available?
A: Absolutely—we design radius bends, multi-panel units, and hybrid configurations.
Q: How do I prevent screen clogging?
A: Proper feed distribution, regular cleaning, and optimal slot sizing minimize blockages.