Media Retention Nozzles, also known as nozzle strainers, v wire nozzle screens, or water treatment collectors, are crucial components in many water and wastewater treatment processes. These Media Retention nozzles are designed to retain filtration media such as sand, anthracite, activated carbon, and ion exchange resins while allowing treated liquids to pass through at the desired flow rate. With a focus on durability, compatibility, and optimal performance, our Media Retention Nozzles are tailored to meet the unique requirements of various industrial applications.
Why Choose Our Media Retention Nozzles?
Our Media Retention Nozzles offer several distinct advantages over traditional filtration components:
1. Exceptional Strength and Durability
Manufactured using high-quality materials, our nozzles are built to withstand the demanding conditions of water and wastewater treatment applications. They are more durable than other materials commonly used in filtration systems, ensuring a longer service life and reducing the need for frequent replacements.
2. High Percentage of Open Area
Our nozzles are designed with a high percentage of open area, which maximizes the flow of treated liquid while retaining the filtration media. This design feature ensures that the filtration process is efficient and effective, maintaining optimal flow rates and reducing downtime due to clogging or blockages.
3. Naturally Anti-Clogging
The unique design of our nozzles prevents clogging, ensuring consistent performance over time. This anti-clogging feature minimizes maintenance requirements and extends the lifespan of your filtration system.
4. Minimal Pressure Drop
Our Media Retention Nozzles are engineered to minimize pressure drop across the filtration system. This ensures that the treated liquid flows smoothly through the system, maintaining consistent pressure levels and optimizing energy efficiency.
5. Versatile Slot Sizes and Configurations
We offer a wide range of slot sizes to accommodate different filtration needs. Whether you require fine filtration for small particles or larger slots for coarser media, our nozzles can be customized to meet your specific requirements.
6. Easy Installation in False Bottom Applications
Designed for easy installation, our nozzles are ideal for use in false bottom applications, where they can be securely mounted and provide reliable media retention. This feature simplifies the installation process and reduces the time and cost associated with setting up your filtration system.
7. Long-Lasting Performance
With a focus on quality and durability, our nozzles are designed to provide long-lasting performance, even in challenging environments. This reduces the need for frequent maintenance and replacement, saving you time and money in the long run.
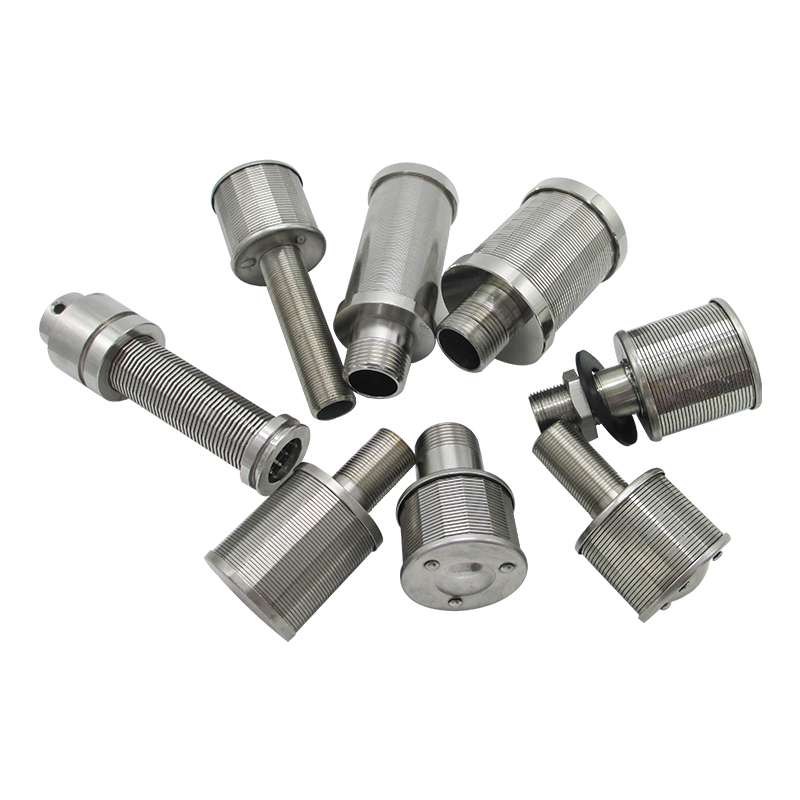
Applications of Media Retention Nozzles
Media Retention Nozzles are versatile components used in a wide range of industries and applications. Some of the most common applications include:
1. Water Treatment
In water treatment facilities, Media Retention Nozzles are used to retain various types of filtration media, such as sand, anthracite, and activated carbon. These nozzles help ensure that the treated water meets the required quality standards by effectively removing impurities and contaminants.
2. Wastewater Treatment
In wastewater treatment plants, Media Retention Nozzles play a critical role in retaining filtration media used to remove suspended solids, organic matter, and other pollutants from wastewater. The nozzles help maintain optimal flow rates and prevent clogging, ensuring efficient and effective treatment of wastewater.
3. Original Equipment Manufacturer (OEM) Applications
OEMs widely use our nozzles in the manufacture of filtration systems and equipment. Their durability, versatility, and high performance make them an ideal choice for use in a variety of OEM applications.
4. Petroleum and Natural Gas Industry
Media Retention Nozzles are used in filtration systems in the petroleum and natural gas industry to remove impurities and contaminants from crude oil, natural gas, and other hydrocarbons. The nozzles help maintain the quality of the product and protect downstream equipment from damage.
5. Power Generation
Media Retention Nozzles are used in power generation facilities to remove impurities from cooling water, boiler feedwater, and other process fluids. These nozzles help ensure the efficient operation of power generation equipment and reduce the risk of damage from contaminants.
6. Food and Beverage Industry
In the food and beverage industry, Media Retention Nozzles are used to filter water and other liquids used in the production process. The nozzles help ensure that the final product meets quality and safety standards by effectively removing impurities and contaminants.
7. Mining Industry
In the mining industry, Media Retention Nozzles are used in filtration systems
remove solids and other contaminants from process water. The nozzles help maintain the efficiency of the filtration system and protect downstream equipment from damage.
8. Pharmaceutical Industry
In pharmaceutical manufacturing, Media Retention Nozzles are used to filter water and other liquids used in the production process. These nozzles help ensure that the final product meets strict quality and safety standards by effectively removing impurities and contaminants.
9. Pulp and Paper Industry
In the pulp and paper industry, Media Retention Nozzles are used to filter process water and other liquids used in the production process. The nozzles help maintain the efficiency of the filtration system and protect downstream equipment from damage.
Custom Manufacturing for Your Specific Needs
Can't find the Media Retention Nozzle you need? Our team specializes in custom manufacturing to meet your specific requirements. With extensive experience in designing and producing high-quality nozzles, our sales, engineering, and production teams work closely with you to develop a solution that meets your exact needs.
We offer a wide range of customization options, including:
Material Selection: Choose from a variety of materials to ensure compatibility with your specific application.
Thread Types: Available in straight or pipe threads, depending on your system requirements.
Connection Types: Our nozzles can be manufactured with different connection types, including crank bolt systems, to suit your needs.
Orifice Design: Nozzles are manufactured according to customer-specific orifice designs, ensuring optimal performance for your application.
Slot Sizes: Various slot sizes are available to accommodate different filtration needs, from fine to coarse media retention.
Screen Diameter and Length: Nozzles are not limited by screen diameter or length, allowing for maximum flexibility in design.
By keeping all manufacturing processes in-house, we maintain strict quality control and ensure consistency and accuracy in every product we produce.
Wedge wire media Retention Nozzles are an essential component in a wide range of water and wastewater treatment applications, providing reliable media retention while allowing treated liquids to flow at the desired rate. Our nozzles are designed for strength, durability, and optimal performance, making them an ideal choice for various industries, including water treatment, wastewater treatment, oil and gas, power generation, food and beverage, mining, pharmaceutical, and pulp and paper.
Partner with YUANLV for Your Filtration Needs
If you can't find the nozzle you need, we specialize in custom manufacturing to meet your specific requirements. Contact us today to learn more about our Media Retention Nozzles and how we can help you achieve your filtration goals.
Call to Action: Contact us today for a quote or to discuss your custom nozzle needs!